The Benefits of a Robust ECM Process for OEMs
“Change is the only constant in life” - These words from the philosopher Heraclitus hold particularly true in the world of engineering and product development. Every new product comes with the need for iterations, revisions and adjustments. How you manage these changes can be the difference between staying ahead or falling behind of the competition. This is where Engineering Change Management (ECM) comes in. ECM is an integral part of product data management to ensure that changes are integrated and executed seamlessly, avoiding confusion, delays, and unnecessary cost.
So, what is Engineering Change Management? It is a structured process put in place to handle product updates, part revisions and modifications during the product development lifecycle. It’s not just about tracking changes, but also ensuring that all potential impacts of a change are evaluated before being implemented, and that all stakeholders are bought in and aligned to the changes. ECM is fundamental to ensuring that your product development stays on course and the changes that need to be included are contributing towards this (rather than derailing it).
For OEMs, the benefits of a well-executed ECM process are huge:
- It reduces delays in product releases by ensuring that every change is properly vetted and approved.
- It minimizes the risk of miscommunication between design, engineering, and manufacturing teams, which can lead to costly mistakes and rework.
- It improves collaboration, by ensuring that everyone operates with the latest, most accurate product data. This eliminates confusion and keeps projects moving forward efficiently.
Our Approach: Progressive Maturity in ECM
ECM is a requirement through the entire product lifecycle. It doesn’t need to be a fully-fledged process during the concept phases, but there are base level requirements that should be met. We call this a Progressive Maturity Approach to ECM.
As the product matures, focus should shift from enabling rapid design iteration to supporting robustness and traceability. During the concept phase only a lightweight process is implemented for version control. However, when you move to prototype and testing (transitioning from the digital to the physical), formal ECM processes must be in place. By the time your product goes into series production, changes should be carefully planned, considering lifetime cost impact and implementation planning.

The key to effective Engineering Change Management (ECM) is having a proactive approach. By anticipating and addressing potential issues early in the development cycle, you can minimize the need for reactive changes and costly rework. Implementing robust data quality monitoring and issue management systems to identify and address potential problems before they escalate will support in this.
Shifting the peak workload of changes to the early stages of development is crucial. Strategies like data freeze deadlines, rigorous requirements change control, and planned release schedules based on milestones and features ensure that issues are addressed before they become major roadblocks.
Finally, one must embrace agile workflows, well-structured change management meetings, and data-driven decision making. These practices allow us to identify and address bottlenecks effectively. Automation will also play a crucial role in streamlining tasks and reducing errors, ultimately leading to faster development cycles and successful product launches.
We suggest implementing a Minimum Viable Product for change management and then working to continuously improve that process. This allows organizations to quickly implement a change management process while supporting the continuous improvement of the business and building ownership and responsibility in the organization.
Proactive Strategies for Effective Change Management
So how do you know if your ECM process needs attention? If you are frequently experiencing project delays, unexpected costs, or quality issues after changes are implemented, it’s a clear signal that something is amiss. Miscommunication between teams, confusion over which design version is the most current, or recurring rework due to poorly managed changes are all red flags. In an OEM environment, these issues can lead to massive disruptions, affecting both your time to market and your bottom line.
Case Studies: Real-World Success Through Effective ECM
Quick Release_ boasts a diverse portfolio of clients, spanning across various industries including automotive, aerospace, defence, rail, and energy. From established global automotive OEMs to burgeoning start-ups, and small-scale luxury automotive manufacturers, QR_ has the experience and expertise to understand the unique challenges of each sector and business regardless of size.
Case Study 1:
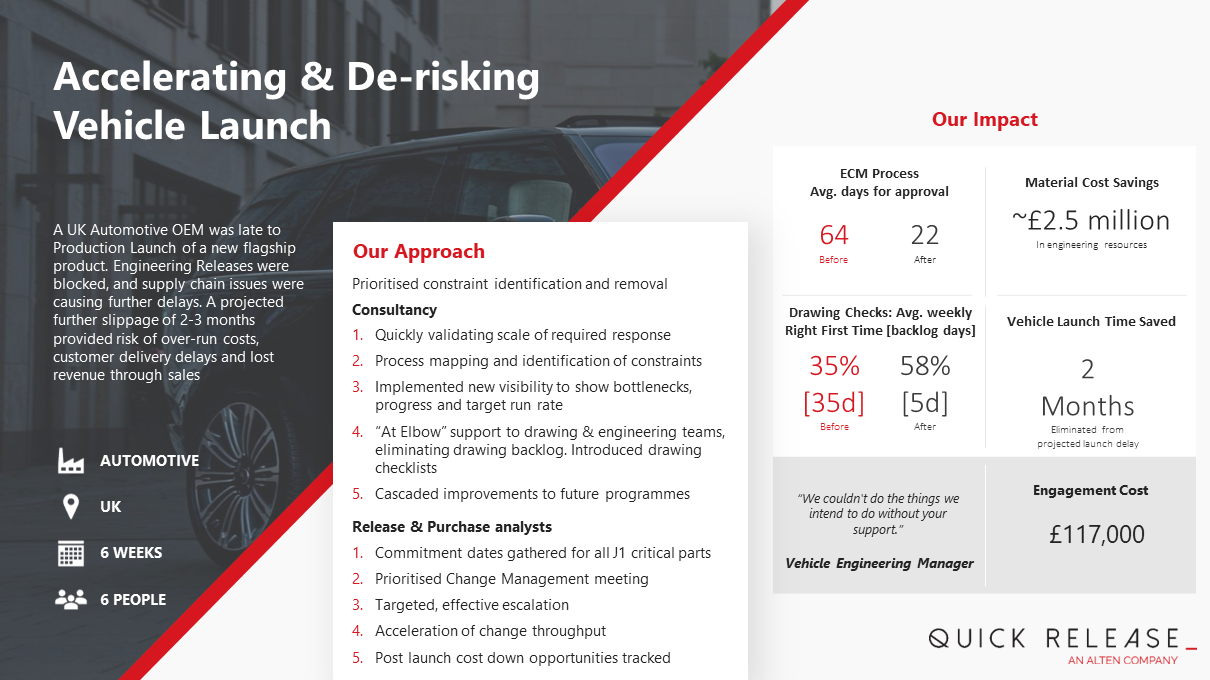
A UK automotive OEM faced a critical situation with their new flagship product: a looming production launch delay. Engineering releases were stalled, supply chain issues were causing further setbacks, and a projected 2-3 month slippage threatened to escalate costs, delay customer deliveries, and result in lost revenue.
QR_ intervened, prioritizing the identification and removal of constraints. Consultancy services validated the scale of the required response, mapped processes to pinpoint bottlenecks, and implemented new visibility tools to track progress and target run rates. "At elbow" support provided to engineering teams eliminated drawing backlogs and introduced drawing checklists. Release analysts gathered commitment dates for critical parts, prioritized change management meetings, and implemented targeted escalation strategies to accelerate change throughput.
The results were impactful: ECM process approval days were reduced from an average of 64 days to 22 days, estimated material cost savings of $2.5 million were achieved, and the vehicle launch was accelerated by two months, avoiding a projected delay. Furthermore, QR_'s intervention established a foundation for cascading improvements to future programs.
Case Study 2:
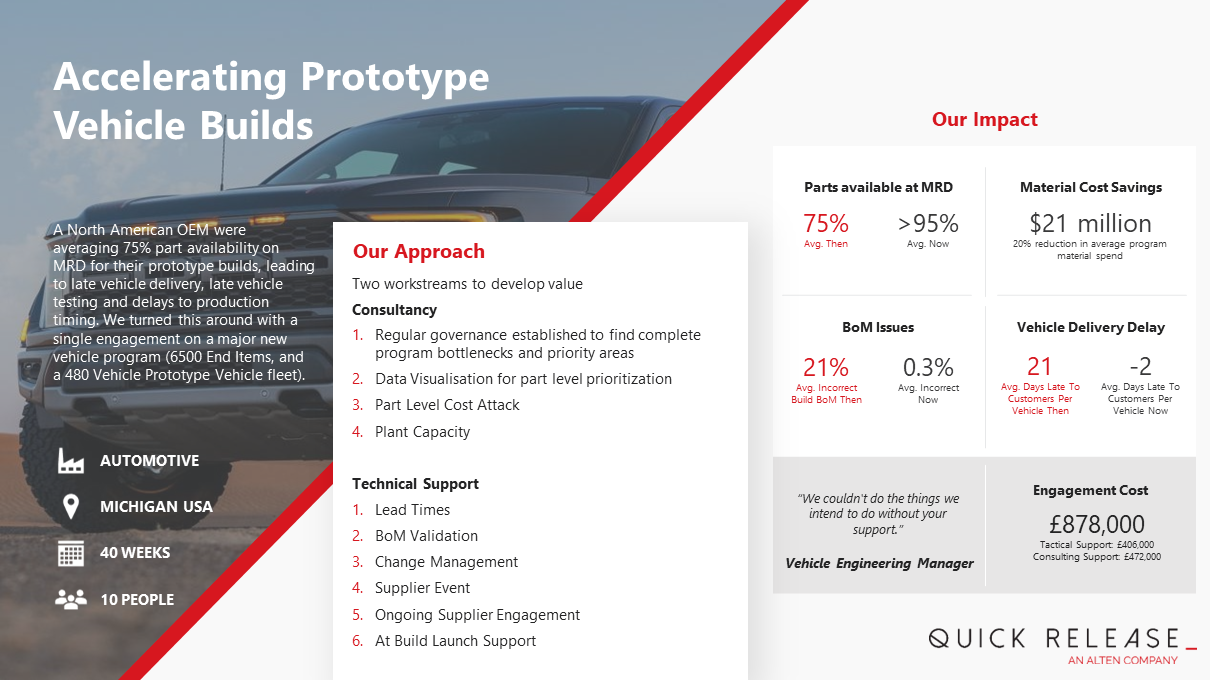
A North American OEM was facing significant challenges with part availability for their prototype builds, resulting in late vehicle deliveries, delayed testing, and production delays. This situation, with an average part availability of only 75%, was a major concern for the company. QR_ stepped in to address this critical issue on a major new vehicle program involving 6,500 end items and a prototype fleet of 480 vehicles.
QR_ implemented a two-pronged approach. First, a consultancy team, which included establishing regular governance to identify program bottlenecks and priority areas, supported data visualization for part-level prioritization and cost analysis workstreams. Additionally, a technical support team focused on lead time optimization, Bill of Materials (BOM) validation, change management, supplier engagement, and providing ongoing support during vehicle build launch. The result was a dramatic improvement: Estimated material cost savings of $21 million were achieved. Part availability at the Material Release Date (MRD) increased from 75% to 95%, BOM issues were drastically reduced, and average delivery delays were cut from 21 days late to 2 days early.
Final Thoughts: Ensuring Success with Proactive Change Management
In the dynamic world of engineering and product development, effective Engineering Change Management (ECM) is not just a good practice, it's a necessity. ECM ensures that changes are seamlessly integrated and executed, avoiding confusion, delays, and unnecessary costs. By implementing a structured process to handle product updates, part revisions, and modifications, ECM empowers OEMs to achieve significant benefits: reduced release delays, minimized communication errors, improved collaboration, and a more efficient product development process.